First thruster prototype test
First thruster prototype test
I received a few parts over the last week so I'm now in a position to do some initial thruster tests.
Motor is a MultiStar Viking 1308-4100KV Brushless Outrunner Drone Racing Motor connected directly to a 60mm Robbe kort nozzle prop with a lock nut on the back.
The motor is rated 200W with a 3S LiPo, but I'm using a 2S for now which should give a max 100W approx.
The initial test was promising, it seems quite powerful though my wiring got hot so I might have to restrict my power to save melting the connectors that I have chosen.
Pics & a short video in the links.
https://flic.kr/p/Q37ggS
https://flic.kr/p/2cbaHbZ
https://youtu.be/FoZxiF49YTY
Motor is a MultiStar Viking 1308-4100KV Brushless Outrunner Drone Racing Motor connected directly to a 60mm Robbe kort nozzle prop with a lock nut on the back.
The motor is rated 200W with a 3S LiPo, but I'm using a 2S for now which should give a max 100W approx.
The initial test was promising, it seems quite powerful though my wiring got hot so I might have to restrict my power to save melting the connectors that I have chosen.
Pics & a short video in the links.
https://flic.kr/p/Q37ggS
https://flic.kr/p/2cbaHbZ
https://youtu.be/FoZxiF49YTY
Re: First thruster prototype test
I've added an acrylic shroud to the thruster, so just a 3D printed pedestal to replace the metal strip and that'll be it finished.
The tube is 70mm O/D, 62mm I/D, and the prop is 60mm.
I made a test jig to measure thrust and got 530g forward and 460g reverse. The prop is not totally symmetrical and so favours forward thrust a little.
Those values are with a 2S battery and somewhere like 50% throttle. I think I'll go to 3S but limit the maximum throttle to restrict the current as this will allow me to use proper subsea connectors for the thrusters without melting the wiring!
Photo & video:-
Thruster with acrylic shroud by Richard the Rogue, on Flickr
https://youtu.be/kaw9NczN6gQ
The tube is 70mm O/D, 62mm I/D, and the prop is 60mm.
I made a test jig to measure thrust and got 530g forward and 460g reverse. The prop is not totally symmetrical and so favours forward thrust a little.
Those values are with a 2S battery and somewhere like 50% throttle. I think I'll go to 3S but limit the maximum throttle to restrict the current as this will allow me to use proper subsea connectors for the thrusters without melting the wiring!
Photo & video:-
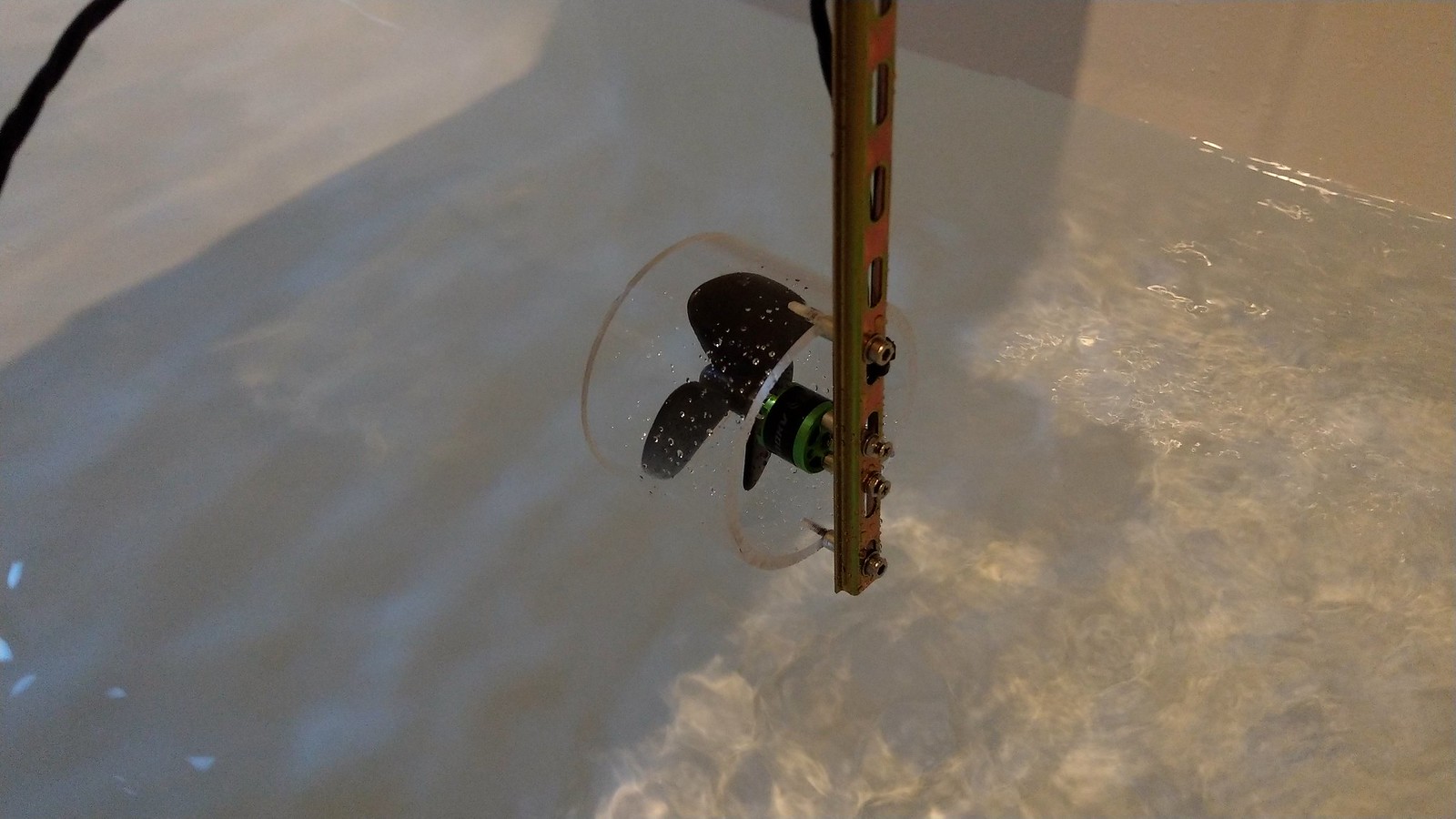
https://youtu.be/kaw9NczN6gQ
-
- Posts: 187
- Joined: Mar 4th, 2018, 6:11 pm
- Location: Valverde de Júcar, Cuenca, España
Re: First thruster prototype test
aunque este tipo de motor te funcione dentro del agua, no es conveniente que este en contacto directo con el agua, porque se terminaran oxidando los componentes interiores, y te puede entrar cualquier cosa que este flotando en el agua, ten en cuenta que la prueba la estas realizando en un cubo con agua limpia del grifo, en un espacio natural, como puede ser un lago o en el mar, en el agua se reparten al 50 %, el h2o, (símbolo químico del agua) y las partículas flotando, cualquier trozo de alga, arena, u otra cosa que se te pueda introducir entre la carcasa del motor y el rotor, puede tener consecuencias nefastas, yo estoy intentando proteger el motor con un tubo de PVC, del que se utiliza en fontanería para el desagüe, todavía no lo he probado en el agua, pero no quiero que se me paren los motores porque se haya metido algo que lo atasque e impida que se mueva, un saludo desde Cuenca España.
Although this type of engine will work within the water, it is not advisable to be in direct contact with the water, because they will end up oxidizing the interior components, and you can enter anything that is floating in the water, keep in mind that the test is Making in a bucket with clean tap water, in a natural space, as can be a lake or in the sea, in the water are dealt to 50%, the H2O, (chemical symbol of the water) and the particles floating, any piece of seaweed, sand, or other thing that you can enter between L A motor housing and rotor, it may have dire consequences, I am trying to protect the engine with a PVC pipe, which is used in plumbing for drainage, I have not yet tried in the water, but I do not want to stop the engines because it has gotten into the Go to jam it and prevent it from moving, greetings from Cuenca Spain.
este enlace te puede servir de ayuda
This link can help you
viewtopic.php?f=18&t=1908
Although this type of engine will work within the water, it is not advisable to be in direct contact with the water, because they will end up oxidizing the interior components, and you can enter anything that is floating in the water, keep in mind that the test is Making in a bucket with clean tap water, in a natural space, as can be a lake or in the sea, in the water are dealt to 50%, the H2O, (chemical symbol of the water) and the particles floating, any piece of seaweed, sand, or other thing that you can enter between L A motor housing and rotor, it may have dire consequences, I am trying to protect the engine with a PVC pipe, which is used in plumbing for drainage, I have not yet tried in the water, but I do not want to stop the engines because it has gotten into the Go to jam it and prevent it from moving, greetings from Cuenca Spain.
este enlace te puede servir de ayuda
This link can help you
viewtopic.php?f=18&t=1908
Re: First thruster prototype test
I bought the motors for less than £7 each, so I'm willing to consider them semi-disposable.
I'll flush them with WD40 after each dive, and they are only for use in fresh water.
I'll flush them with WD40 after each dive, and they are only for use in fresh water.
Re: First thruster prototype test
Ok so I finally got round to testing my thruster with the 3D printed pedestal and a 3S battery.
I tried it last week and the thruster tore my test jig to pieces. Well, it was already cracked...
Anyway, I tried again just now and I'm getting almost exactly 1kg of thrust from it. It plateaus at just under 50% throttle, which I'm assuming is because of the relatively high torque that the motor is experiencing. A propeller with a shallower pitch would be of help.
Worryingly, the motor controllers (Hobbyking 30A car ESCs) get VERY hot very quickly and cut out! I'm hoping that it might be at least partly due to the too thin wire that I'm using between ESC and motor in my test jig. That also gets very hot, so I think it is leading to excessive current draw.
Anyway, I'm happy with the 1kg thrust and I suppose I'll just have to re-scale my joystick inputs to match the restricted throttle range. I'm also happy that the pedestal didn't break, which was really the point of the test in the first place.
I tried it last week and the thruster tore my test jig to pieces. Well, it was already cracked...
Anyway, I tried again just now and I'm getting almost exactly 1kg of thrust from it. It plateaus at just under 50% throttle, which I'm assuming is because of the relatively high torque that the motor is experiencing. A propeller with a shallower pitch would be of help.
Worryingly, the motor controllers (Hobbyking 30A car ESCs) get VERY hot very quickly and cut out! I'm hoping that it might be at least partly due to the too thin wire that I'm using between ESC and motor in my test jig. That also gets very hot, so I think it is leading to excessive current draw.
Anyway, I'm happy with the 1kg thrust and I suppose I'll just have to re-scale my joystick inputs to match the restricted throttle range. I'm also happy that the pedestal didn't break, which was really the point of the test in the first place.
Re: First thruster prototype test
Six thrusters good to go.
I'm thinking of wet-running the motor controllers too, to cool them.
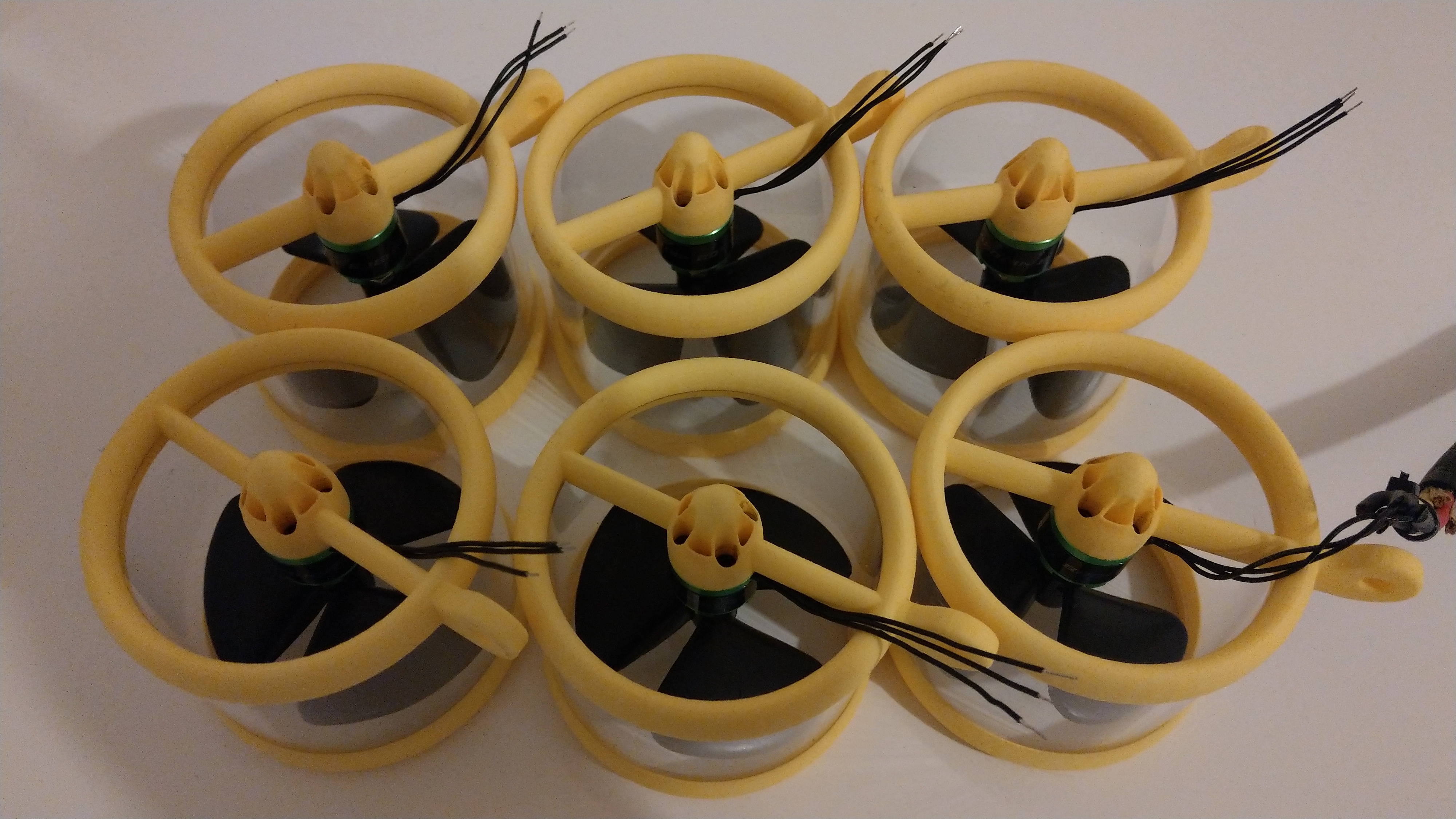
I'm thinking of wet-running the motor controllers too, to cool them.
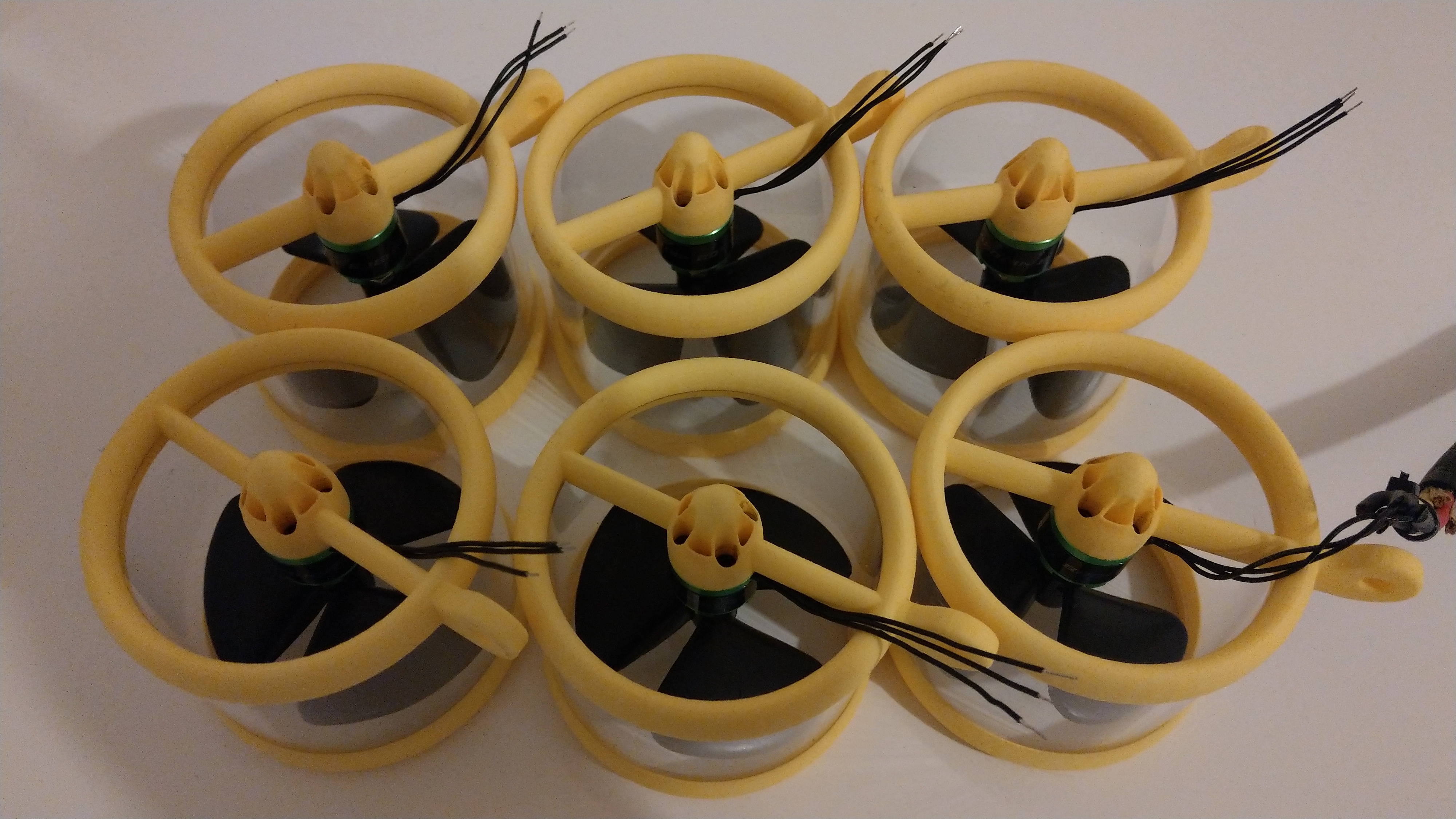
Re: First thruster prototype test
Um...In the beginning you said these were 4100kv motors...
The lower the KV, the higher the torque. Quadcopters need high-speed, low torque motors to drive the props in air. ROV's need medium-speed, high-torque motors because they drive big fat-bladed props in water.
I'd imagine the reason your 30amp ESC's are overheating is because they are trying to supply tiny motors turning big props...in water.
Try your thrust test again with a 2200kv or 1100kv motor. I'll bet your ESC's run much cooler, and you'll get more thrust as well.
I personally use 400kv motors but my ROV is HUGE.
To waterproof your ESC's (or LED's), coat them in 5-minute epoxy thinned with denatured alcohol.
The lower the KV, the higher the torque. Quadcopters need high-speed, low torque motors to drive the props in air. ROV's need medium-speed, high-torque motors because they drive big fat-bladed props in water.
I'd imagine the reason your 30amp ESC's are overheating is because they are trying to supply tiny motors turning big props...in water.
Try your thrust test again with a 2200kv or 1100kv motor. I'll bet your ESC's run much cooler, and you'll get more thrust as well.
I personally use 400kv motors but my ROV is HUGE.
To waterproof your ESC's (or LED's), coat them in 5-minute epoxy thinned with denatured alcohol.
Re: First thruster prototype test
You are of course correct. My problem was always finding high torque motors of about the right size. In a way, the decision to use these motors came from the limited kort nozzle prop choice available to me. Turns out that I can run them at 45% throttle and get a maximum of 1kg thrust from each, which I think is sufficient for an ROV of this size.Oddmar wrote:Um...In the beginning you said these were 4100kv motors...
The lower the KV, the higher the torque. Quadcopters need high-speed, low torque motors to drive the props in air. ROV's need medium-speed, high-torque motors because they drive big fat-bladed props in water.
I'd imagine the reason your 30amp ESC's are overheating is because they are trying to supply tiny motors turning big props...in water.
Try your thrust test again with a 2200kv or 1100kv motor. I'll bet your ESC's run much cooler, and you'll get more thrust as well.
I personally use 400kv motors but my ROV is HUGE.
To waterproof your ESC's (or LED's), coat them in 5-minute epoxy thinned with denatured alcohol.
Looking at it another way, it's about matching propeller to motor, and what I need is a smaller prop or a lower pitched prop.. I may spend more money and time testing when I have more money and time.
I was going to waterproof the ESCs with a few layers of PCB lacquer.
Re: First thruster prototype test
Maybe put this gearbox on your motor?
https://www.amazon.com/dp/B0745VWJ54/ref=dp_cerb_1?th=1
For my own ROV, I figured just Having the prop ducted was more important than a perfect 'kort' shaped nozzle, so i just cut a ring from PVC and sharpened the edges. Of course MY PVC rings are 8" diameter...
For T200-type props, have you considered getting an EDF 6-bladed prop and cutting off 3 blades?
https://www.amazon.com/JFtech-6-Blade-P ... B07C2BST4M
https://www.amazon.com/dp/B0745VWJ54/ref=dp_cerb_1?th=1
For my own ROV, I figured just Having the prop ducted was more important than a perfect 'kort' shaped nozzle, so i just cut a ring from PVC and sharpened the edges. Of course MY PVC rings are 8" diameter...

For T200-type props, have you considered getting an EDF 6-bladed prop and cutting off 3 blades?
https://www.amazon.com/JFtech-6-Blade-P ... B07C2BST4M
Re: First thruster prototype test
It's little bigger diameter than my motors, which are only 13mm. Also wet-running a gearbox isn't quite as sensible as wet-running a brushless motor.Oddmar wrote:Maybe put this gearbox on your motor?
https://www.amazon.com/dp/B0745VWJ54/ref=dp_cerb_1?th=1
My cowlings are really just ducts, not proper Kort nozzles, however the reason for choosing a Kort blade was largely down to reducing tip vortex losses and getting a reasonably symmetrical prop that didn't overly favour forward or reverse direction.Oddmar wrote:For my own ROV, I figured just Having the prop ducted was more important than a perfect 'kort' shaped nozzle, so i just cut a ring from PVC and sharpened the edges. Of course MY PVC rings are 8" diameter...
A proper Kort profile doesn't actually help a bi-directional thruster as used on ROVs. It can however provide a small efficiency improvement for boats when forwards is the primary direction of travel. To my mind, the primary function of an ROV thruster cowling is to stop the tether getting chewed up!
I looked at ducted fans but only looked at complete assemblies. I reasoned that they were even higher Kv than what I ended up using, plus the propellers were designed for use in air, not water, so they would be even less optimal than my setup.Oddmar wrote:For T200-type props, have you considered getting an EDF 6-bladed prop and cutting off 3 blades?
https://www.amazon.com/JFtech-6-Blade-P ... B07C2BST4M
Whilst chopping blades off a ducted fan prop might work, the blade angles look rather steep and I'm not sure the end result would be any better than what I have. It would be an interesting side project though.
I have had some thoughts regarding how these brushless motors work in an ROV thruster configuration, and have come to the conclusion that although the perfect setup is hard to achieve with off the shelf components, the result that I have achieved is not too bad. I may post more on this later.
Short version, I'm achieving maximum torque, but almost certainly at below the optimal RPM, and therefore at less than peak power / efficiency.
I could improve this with a better matched prop, which means a smaller diameter / shallower pitch. Again, an interesting side project.