Page 1 of 1
Acrylic/aluminum hull problems
Posted: Feb 24th, 2016, 7:09 pm
by puzzler300
Hi all,
I've been working on building a hull for my electronics. This is my 3rd iteration, and the one I'm most confident about. I'm working on the primary housing --housing my camera, batteries, and Arduino-- and so far it looked like it was going pretty well.
It's primarily made out of a 3" (76.2mm) ID 3.5" (88.9mm) OD acrylic tube. The ends are machined aluminum with 2 3" (76.2mm) ID 3.5" (88.9mm) OD o-rings, one on each end. The white brackets on the ends serve only to hold the end caps in place by means of four threaded rods. I tested it in my bathtub just to make sure the idea wasn't fundamentally flawed and that worked really well, actually. I took a trip to the pool at my university and threw it in the deep end and I'd say it lasted 6' (1.8m) before it started leaking.
I feel pretty stumped as to where to go from here. Any input would be greatly appreciated!
Re: Acrylic/aluminum hull problems
Posted: Feb 24th, 2016, 8:59 pm
by puzzler300
I'm adding a CAD drawing that might help clarify what how the tube end works
Re: Acrylic/aluminum hull problems
Posted: Feb 24th, 2016, 9:33 pm
by Jarubell
To start, I have no experience and yet to even start building.
How straight are the cut ends? How did you prep them?
Re: Acrylic/aluminum hull problems
Posted: Feb 24th, 2016, 9:41 pm
by puzzler300
Approximately straight? I haven't done anything to it. I bought it off McMaster Carr and just left it. Definitely has saw marks on the ends, no idea the depth, but I can feel them. I want to put it in a lathe and face it, but I also don't want to shatter it (if it isn't evident, I have no idea how to work with acrylic).
--edit--
I found this video:
https://www.youtube.com/watch?v=QhAXbA2lmnE and I think I'll try the sander + buffing wheel tomorrow and test it one more time.
I'll post results
Re: Acrylic/aluminum hull problems
Posted: Feb 25th, 2016, 12:22 am
by TigerShark
Clean those ends up and that might work. You could swirl it on fine sandpaper over a very flat surface. Also you might need more compression.
Re: Acrylic/aluminum hull problems
Posted: Feb 25th, 2016, 12:35 am
by puzzler300
Sounds good, I tightened it today until it sounded like the ABS was cracking, but I might try a bit more.
--edit--
I've stripped out the threads on my aluminum threaded rod, any good places to get threaded stainless rod?
Also, has anyone tried silicon grease on their o-rings to help with sealing?
Re: Acrylic/aluminum hull problems
Posted: Feb 25th, 2016, 4:21 pm
by TigerShark
You also shouldn't need to get it that tight. You definitely need to use some grease. I use vasoline. Just a little to moisten the o-ring. You have to keep the area very clean also. I think if you had a part of the end cap that extended into the tube that would work better. I have double O-rings on my setup. One with a seal inside the tube and one seals on the end of the tube. You have to think where is the o-ring going to go when water pressure is squeezing it? I think yours would likely get pushed inside with your current design if you take it too deep.
Home Depot should have threaded rod. You could also get unthreaded and use a die to thread just the ends which would be stronger. You can also order it from Mcmastercarr.com or onlinemetals.com
Re: Acrylic/aluminum hull problems
Posted: Feb 25th, 2016, 11:43 pm
by puzzler300
I was thinking the easiest thing to do would be to re-machine the aluminum caps with a taller center piece, or deeper o-ring grooves. Is there any advantage to the double o-ring system other than redundancy?
Also, do you think plain threaded rod will work? I'm mostly worried about corrosion.
Re: Acrylic/aluminum hull problems
Posted: Mar 2nd, 2016, 8:05 pm
by TigerShark
Here is how my end cap seals:
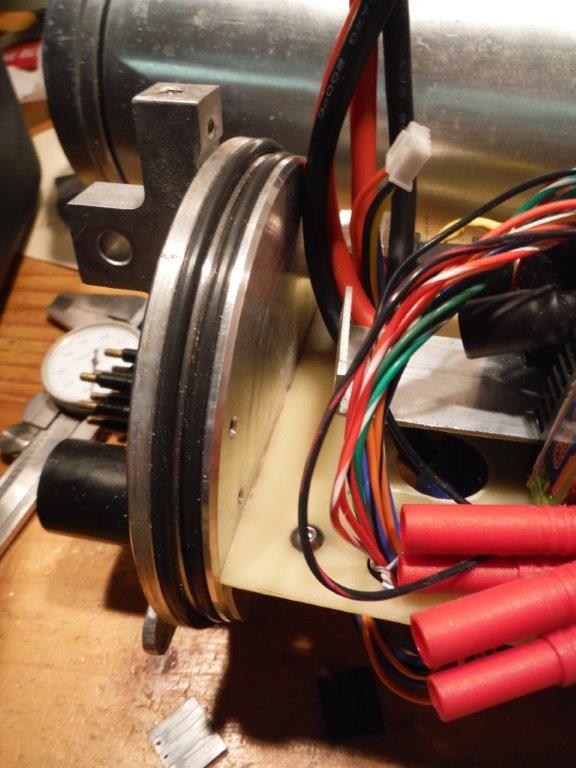
- DSCF6548.jpg (66.83 KiB) Viewed 6890 times
This works for me, I have never had an issue with this design.
I think your rods would be fine but I would use SS or Brass. You could thread just the ends of solid rod.